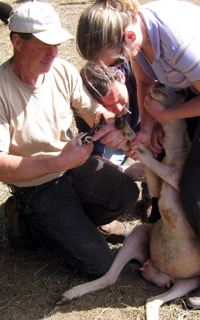
One of the most satisfying days of the year at Chassagne is The Shearing. This occurs anytime after the lambs are born and are independent enough to manage for a few hours without being with their mothers. Usually the shearing takes place in June or July and experience has shown that a crew of at least six or seven able-bodied people plus the shearer works best. Many people shear their sheep up to one month before the birthing but the Shetlands seem to hold onto their wool naturally well into the late spring. If sheared too early such as in April or May the shearer will complain that the wool is too “sticky” (sticking tightly to the body and difficult to remove). By late June the wool is literally starting to fall off the sheep and is much easier to remove as the Shetland has retained the primitive tendency to moult. Before the invention of shears, the sheep were plucked or “rooed”, a Scandinavian word for plucking, and this tradition was still carried out on the Shetland Island until about forty years ago.
In the early morning hours as we start the process there is always a lot of noise as the ewes are herded into the chambers and chute, lining up to be sheared. The shearer we use and admire is Don Metherall, a champion shearer who is most pleasant to work with. He is fast, thorough, careful and friendly. Almost annually Don competes in international shearing championships. As it turns out, the fastest shearers in the world are the New Zealanders capable of shearing more than eight hundred sheep in an eight hour period, but they are challenged by the Welsh, the Scots, and now the Canadians. The record for hand shearing sheep with hand clippers is fifty sheep in eight hours held by a Hungarian so clearly the invention of electrical clippers changed the shearing profession.
But speed is not really too desirable when you are shearing sheep with prized wool…rather you want a good thorough job with the fleece coming off in one joined piece rather than bits and pieces As a sheep is presented to him the shearer will lift the animal up and back onto its haunches thereby rendering it immobile. The clipper blades are very sharp and in the same pattern each time the shearer cuts downward so as not to nick the skin, often holding taut the skin ahead of the clippers in preparation. A good shearer uses long strokes rather than a lot of little short cuts that result in the wool fibres being broken into short pieces….there are no “short cuts” in shearing. A good shearer is in high demand and we have to book him several months in advance. It is back-breaking work and the shearer is the Boss on Shearing Day. The shearer wears special clothing such as moccasin-style shoes that are comfortable and have a natural grip, a wide belt, a muscle shirt and stretchy pants.
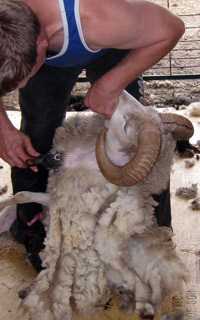
The sheep are corralled into pens and funnelled into a chute so that one is on stand-by to be handed to the shearer as soon as he has finished with the last one. A rhythm is established as the team processes 130 animals in a six or seven hour day, stopping only for a relaxed lunch and one or two brief breaks as the shearer changes his blades. Each fleece is scooped from the plywood floor as soon as it is completely removed from the animal, and the shearer’s work surface is kept swept clean. The Shetland is prized for its lovely wool and easily each animal yields 2½ to 5½ pounds of wool each year… enough to knit one or two adult sized sweaters. The freshly sheared fleeces are placed on a “skirting table” for “skirting”, the term used for removing by hand the hay, debris and soiled bits. The fleece is folded in three lengthwise, rolled like a sleeping bag, and placed in separate bags with a label . Already the finest fleeces showing exceptional “crimp” (the kinkiness of the fibre) and a good “staple” (length of the fibre) are set aside in a special place.
Meanwhile each animal is given annual inoculations, gets a thorough examination, has its feet trimmed, and observations about wool quality and health are recorded. We are so fortunate to have several friends who take a day off their regular work in order to help out.
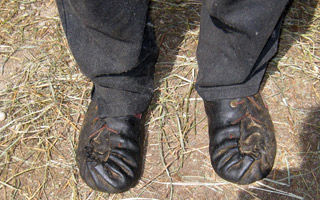
Many fleeces are taken to local woollen mills to be processed into yarn. It used to be difficult to find a mill but just lately three excellent small private mills have been opened by fibre enthusiasts, each owners of alpacas or sheep, so this renewed interest in natural fibres has taken a great turn in popularity in the past five years. During this process the wool is washed and spun. For every pound of raw fleece, one ends up with half of a pound of yarn. Other fleeces are sold to hand spinners who “card” (comb) and spin the fleece “in the grease”, choosing to spin the fleece in its natural state while the lanolin in the fibre helps to lubricate the spinning and then washing the fibre afterward. In the Shetland tradition the wool was not scoured until after being spun and vegetable oil was added using a feather as a brush before the wool was carded by hand into a “rolag”, a sausage shape of wool. In order to dye the wool it was placed in vats of boiled lichens, was brought to a boil for an hour and then left to soak in stale, lukewarm urine for up to three weeks in order to achieve rich, brown tones suitable for Harris tweeds.